Examples of ROSS/FLEX® Solutions
ROSS can repackage the existing, proven internal parts of standard products to your specifications, eliminating the need for life cycle testing. ROSS’s engineering design team can provide a unique solution that is designed to your requirements, delivered in days rather than weeks or months. At ROSS we want to ensure your needs are met quickly for an efficient turnaround, because we know waiting on a solution is valuable and wasted time. There are also no worries about being tied to one supplier for integration with all your other units as the ROSS/FLEX® service can design and manufacture for compatibility with any brand. Some examples of what ROSS/FLEX® does:
- Combining multiple functions into one body
- Adaptor plates to replace non-performing products
- Customised port and pilot locations
- “Building Block” options with different types of stations
- Complete air distribution systems
Have a Project In Mind? Contact ROSS/FLEX® to Get It Started!
Contact UsROSS/FLEX® Examples
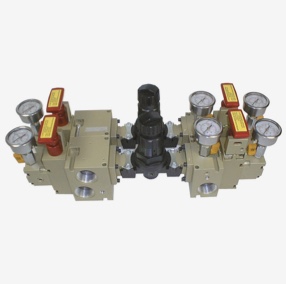
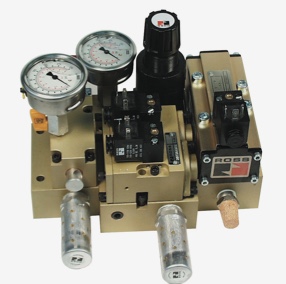
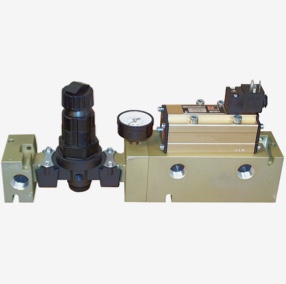
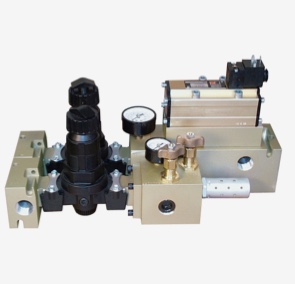
Our Process Using ROSS/FLEX®
ROSS brings you into the process to produce better solutions for your pneumatic applications. ROSS/FLEX® supports your goals and specifications with a specially trained and equipped design engineering team and a fully-automated manufacturing system that is truly “state-of-the-art.” The net result is a unique system solution manufactured to your requirements and developed to your schedule. It’s a special approach, involving some very unique capabilities, which are available only at ROSS.
1-2 WEEKS
3-4 WEEKS
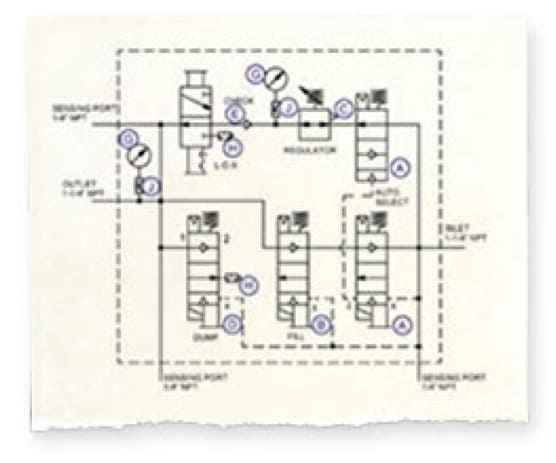
Existing or New Circut

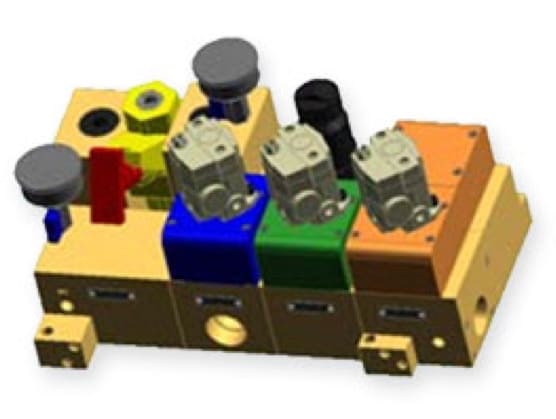
CAD Concept

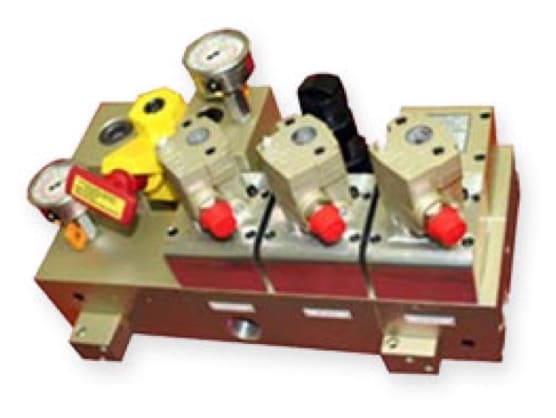
New ROSS System
Continuous Improvement Using ROSS/FLEX®
- Rapid Response Time (from idea to installation)
-
Match any Valve Interface (replace underperforming valves)
- 100% interchangeable, no piping changes Increase uptime & productivity
-
Customer-directed new products
- Mill Engineers work closely with ROSS Engineers using proven ROSS valve technology
-
New Applications or Circuits (optimize and modernize)
- Exact flows and speeds Eliminate piping, reduce leaks Cylinder & valve integration Real-time feedback control Ergonomic and operator-friendly
ROSS/FLEX® - Poppet Valves
At ROSS, we offer innovative solutions and unsurpassed pneumatic technology with proven Solenoid Pilots and Poppet Valve designs. Through ROSS/FLEX® these solutions are delivered quickly for improvement in productivity and reduced costs in the harsh steel mill environment beyond heavy-duty construction.

ROSS poppet valves have positive sealing with no sliding action to prevent damage and wear. They are also self-cleaning and dirt tolerant thanks to the smallest flow-through area across the poppet’s seal and seat which produces a high-enough velocity to blow out all dirt and foreign matter. Plus, the valve is self-compensating.
Poppet Valve Design:
- Perpendicular Face Sealing Poppets (a true poppet)
- Positive Sealing throughout service life (minimal to zero leakage)
- Self-compensating seals (long service life)
- Self-cleaning valve design (increased uptime)
- Positive Shifting due to large differential poppet areas (no sticking)
Helping You With Machine Safety or Machine Guarding
ROSS employs a team of Global Industry Specialist with Vast Experience in fluid power applications with a special emphasis on Safety. The ROSS Safety Team participates in industry standards committees that set policies and best practises for machine guarding in order to improve worker Safety, reduce the likelihood of equipment damage, and increase productivity.
Learn MoreContact Us
Whatever your need, our engineers at ROSS EUROPA would be happy to help you find a solution. Being able to meet industry needs and business specifications is no problem! Contact us to get started on your way to a safer solution with increased productivity!